Plastic Pyrolysis Plant with CE & ISO
Certificate
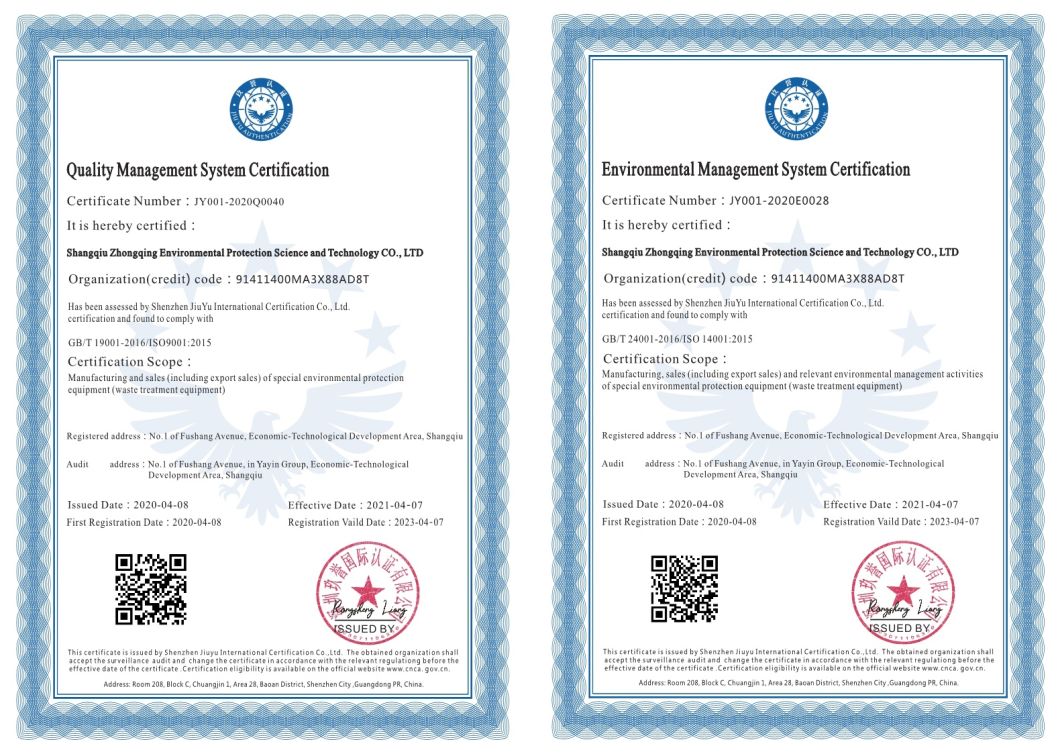
Company Brief Introduction
Shangqiu Zhongqing Greentech Co,.Ltd is a professional institution engaged in the recycling and utilization of waste resources which includes scientific research, design, development, manufacturing, installation, commissioning, training and customer service. The headquarter of the company is located in Beijing. Our main equipment is waste tires equipment, waste oil sludge treatment equipment, living garbage equipment, electronic waste equipment, medical waste equipment, petrochemical waste equipment and related waste recycling equipment. We also undertake government environment project like engineering design, construction and testing date.
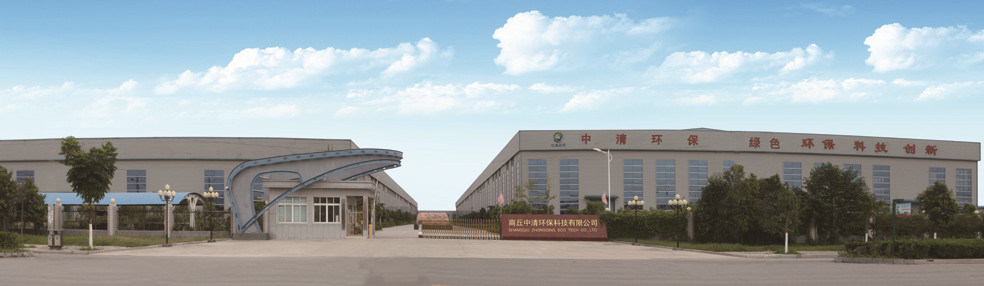
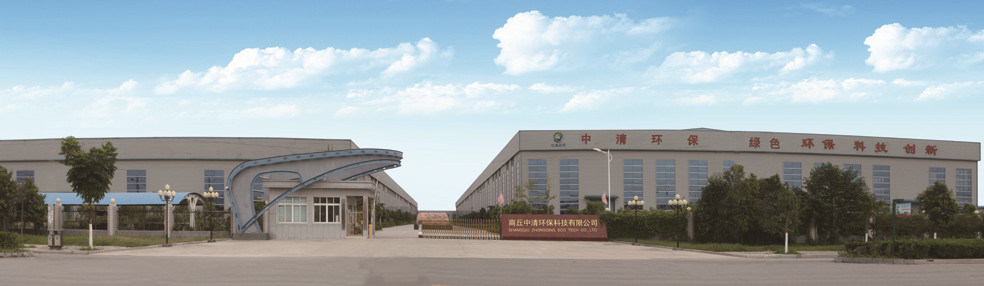
Product Description
1. Waste plastic pyrolysis plant consists of five main system: pyrolysis system, heating system, cooling system, gas recycling system and smoke scrubber system.
1). Pyrolysis system: reactor
----The waste tyre, rubber and plastic can be cracked and be gasified in the reactor
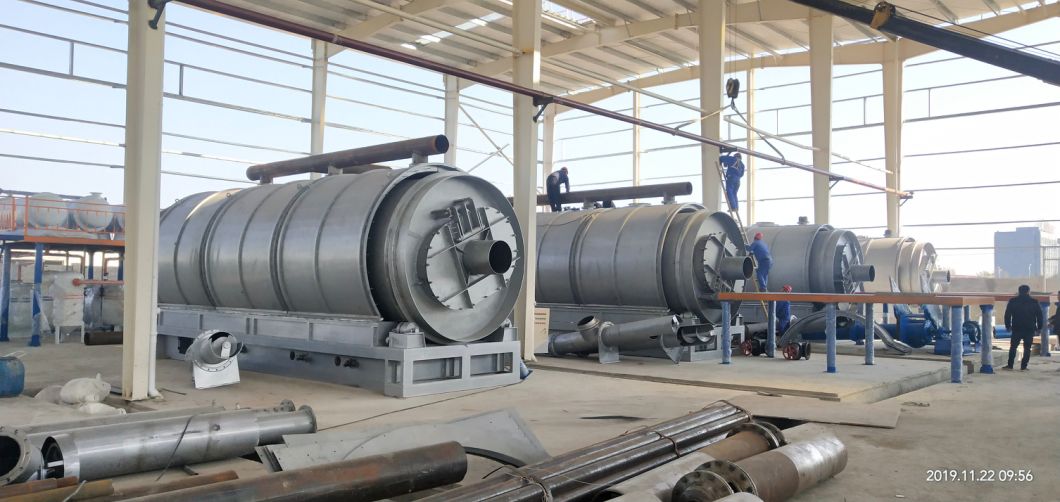
2). Heating system: with sync gas and oil burning burners, blowers, etc., directy heating
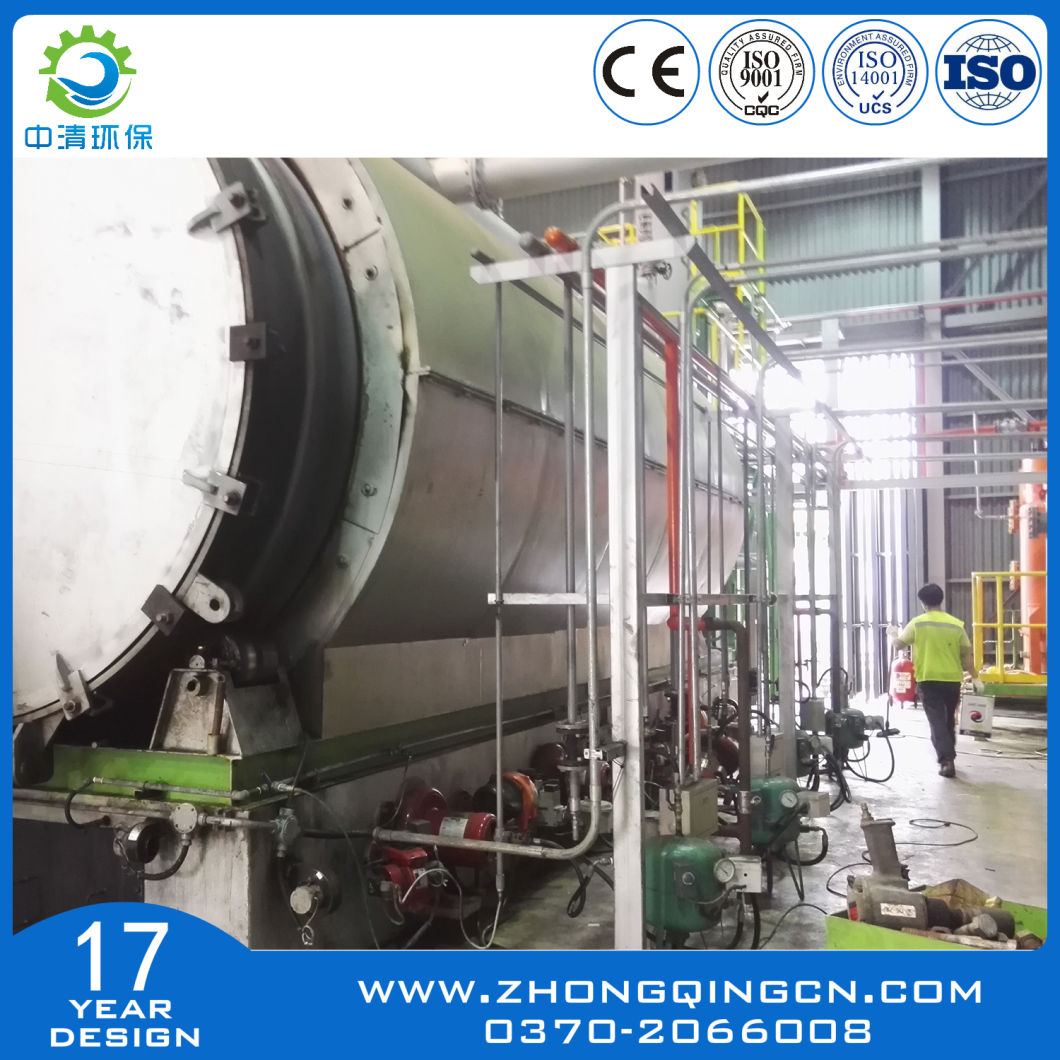
3). Cooling system: condensers, cooling pool and cooling tower
---4 vertical condensers to convert the oil gas into oil
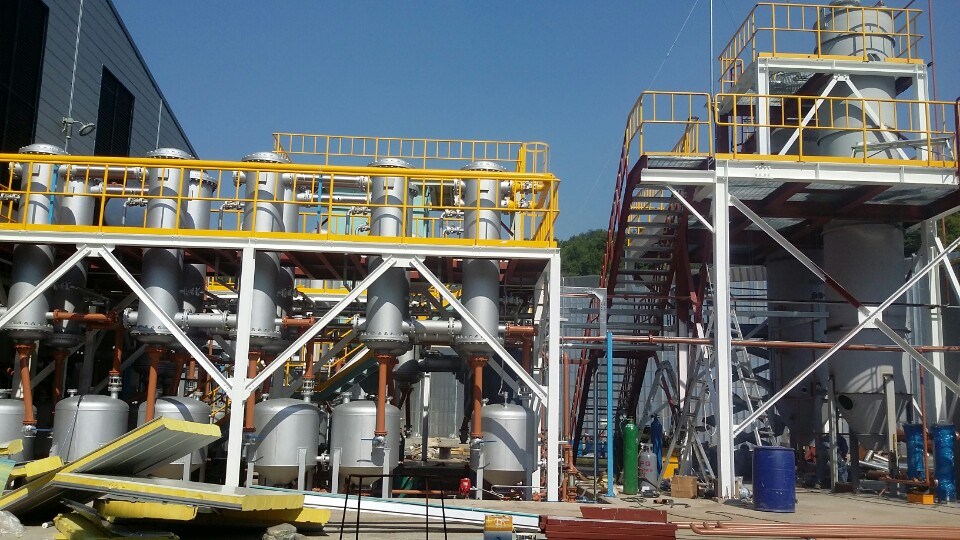
4). Gas recycling system:
----The function of this system is to recycled the gas which cannot be liquefied for buring as fuel
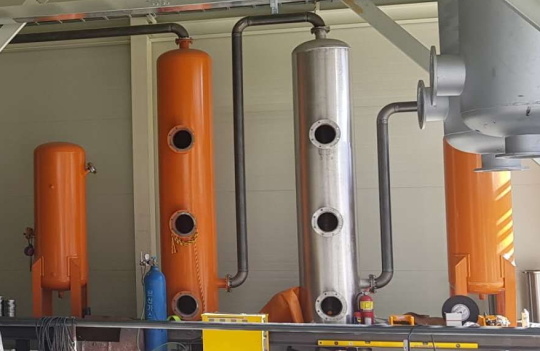
5). Smoke scrubber system:
---its function is to remove the acids, bad smell and dust from the waste gas, so the gas will be more clean and environmental friendly.
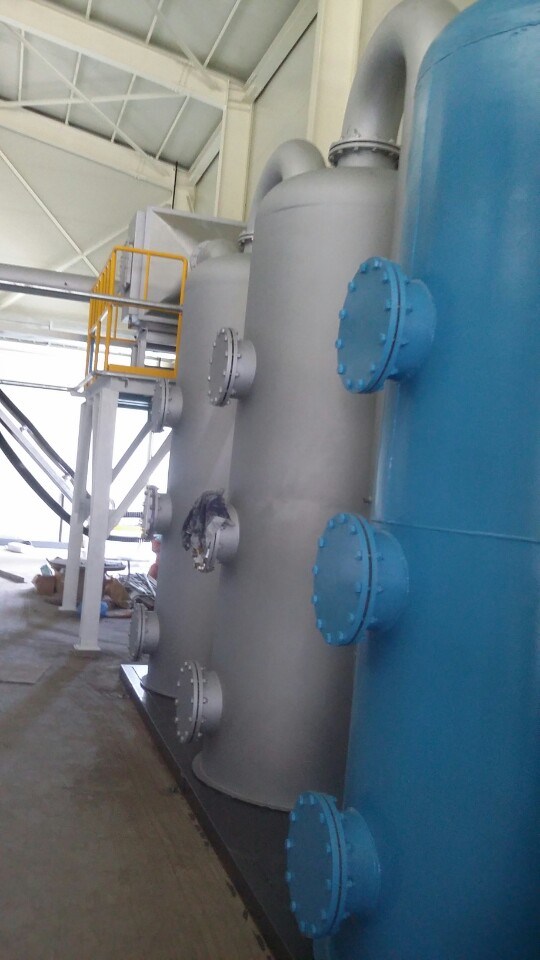
2.Outstanding Features of the Waste plastic pyrolysis plant:
2.1.:Better security. The biggest safety hazard of the pyrolysis plant lies in the possibility of explosion and fire. And the two security risks are all caused by excessive pressure, so how to deal with it?
Our company adopts the prevention method, that is, we won't allow the pressure to be too high; the other companies adopts the treatment method after the pressure is higher, that is, when the pressure has been too high, the safety valve installed at the rector door would be driven to be exploded due to high pressure to carry out the pressure for emergency relief. The disadvantage of this method is that even if the pressure leaks out of the reactor, the possibility of fire occurs at the same time with the occurrence probability as high as 90% or more. And the fire will in turn affect the main reactor.
The preventive measures adopted by our company are: to ensure the smoothness of the pyrolysis operation and the pipelines at all times, and to prevent plugging and leaking; if there is no blockage, the pressure will not suddenly rise, and there will be no reactor explosion or fire without pressure!
As well as the emergency relief valves equipped in other locations, the water seal anti-tempering safety device, etc. are conventional configurations and will not be described here.
2.2: High oil yield and good oil quality: Other companies often have residual oil tanks or heavy oil tanks, and each batch production will produce 100kg~400KG residual oil or heavy oil. This kind of residue oil is very viscous and very dark in color, cannot be sold directly or sold at very low prices. If you mix this residue oil with good quality fuel oil, it will lower the quality of the oil and lower the price. If you throw away it is kind of waste and will pollute the environment. If it is extracted and put into the pyrolysis reactor again for cracking, it will waste labor and the process is dirty.
The anti-blocking device used by our company rotates counterclockwise during production, and the residual oil and other impurities separated from the gas separation package can be pushed back into the reactor for secondary cracking until all high quality oil extracted. The impurities are partially dried to powdery carbon black. Therefore, in one batch, the oil production rate from our machines is 1% to 4% higher than that from other companies; at the same time, it removes the secondary treatment of residual oil and possible pollution problems.
At the same time, the technology of this invention patent reduces the rate of the phenomenon of carbon black rising due to the rotation of the reactor in the production process by more than 90%, which makes the carbon black content in the oil greatly reduced, improves the quality of the oil.
2.3:The equipment pipeline cleaning period is greatly extended: the anti-blocking system adopted by our company ensures the cleanliness of the pipeline while restraining the carbon black from entering the pipeline, which makes the cleaning cycle of our equipment doubled compared with other equipment, which saves Human resources, in turn, enable the equipment to continue to operate.
2.4: Our equipment has better sealing performance: the sealing performance lies in two aspects, one is the sealing at the reactor door and the other is the sealing at the air outlet location. In terms of reactor door, our design is more reasonable and elliptical, and the door is reinforced several times. No matter which kind of raw material is fed, this design can balance the convenience of full door opening and reduce the possibility of door deformation. The elliptical design allows the high-quality packing to slowly change direction when the corner seal is made, the packing structure does not change, and the small square or round door is not convenient to feed the materials, and second the packing is suddenly changed, which makes the structure become slack and is prone to air leakage.
Our reactor door is made of anti-deformation material and design, it will not be deformed, drooping or tightly sealed for a long time.
2.5: Anti-stick and automatic clearing device: Our equipment adopts heat treatment and filming process on the inner wall of the reactor before the first usage, so that the coating agent can penetrate into the steel of the furnace wall to form a plated film, which can prevent the reactor wall from sticking together, avoid flash explosions. The automatic clearing machine adopts the chain scraper structure, and the clearing is more thorough.
2.6:Equipment quality: first, the materials used is really national standard furnace steel, no non-standard materials.
The second is the welding process: our company adopts automatic welding process, no trachoma, and the welding surface is neat and beautiful.
2.7: After-sales service: The equipment is maintained for life. If there is any problem, the confirmation reply will be given within 24 hours after the sale, and the 48-hour personnel will start the on-site service in China or begin the preparation to apply for visa.
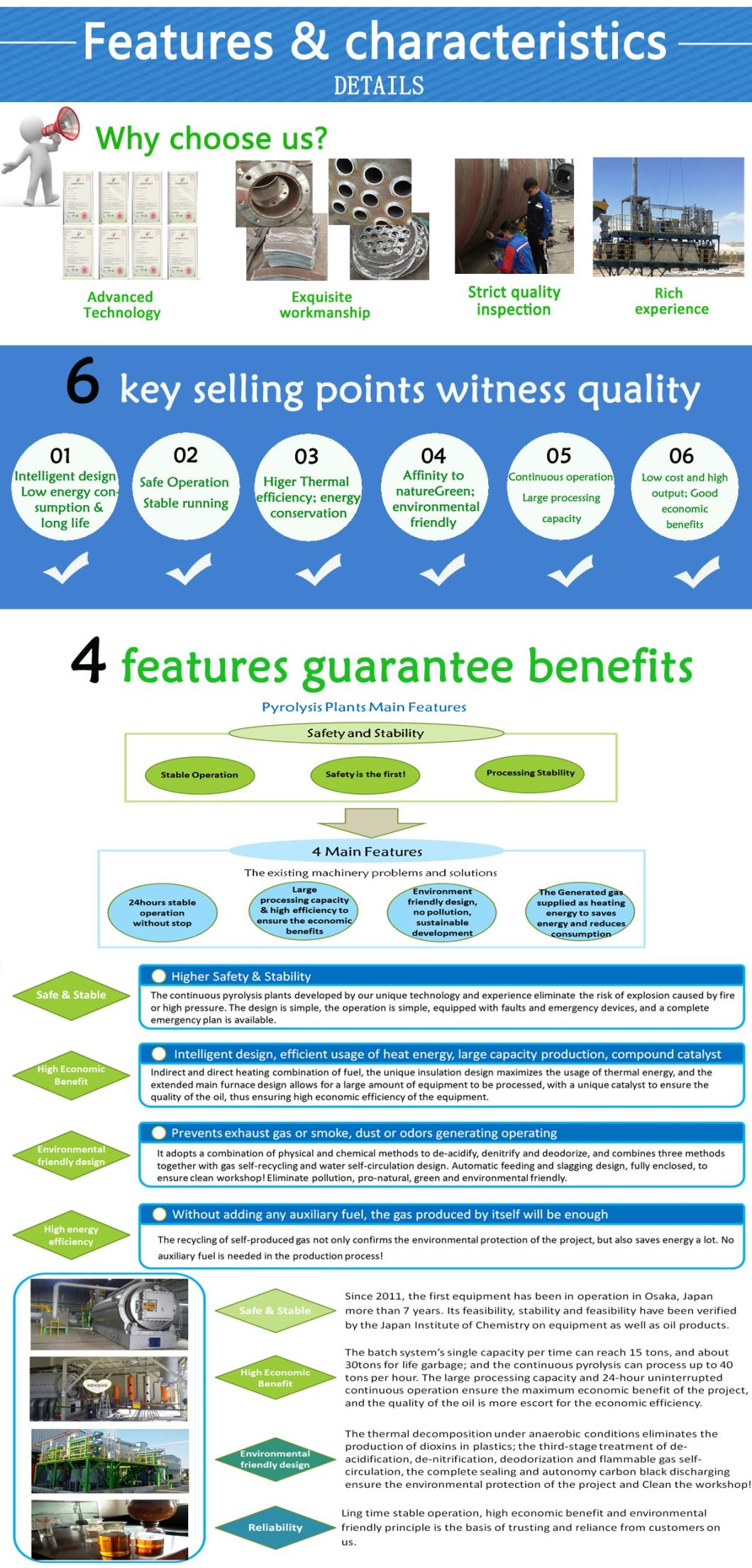
3. Process time of the Waste plastic pyrolysis plant:
Process Time of 10 tons Pyrolysis Plant | |
Feeding | 1~2h |
Heating | 9~10h |
Cooling | 3~4h |
Discharging | 1~2h |
Steel Pulling Out | 20minutes |
4.Final products: Steel wires, fuel oil, carbon black and sync gas...
The usage of the final products:
Steel wires: 12%-15% from tyres, to be sold or reprocessed.
Fuel oil: Widely used in industries such as steel and iron factories, ceramics
or chemical industries or hotels, restaurants etc. as fuel oil, or used
for heavy oil generators to get electricity.
Carbon black: Crude carbon black can be used for construction bricks, or widely
used as industrial carbon black N774, N660, N330 or color carbon after
deep-process.
5.Feasibility Analysis for your reference:
Note: A. This analysis is made with capacity of 10Mt tyres per day per batch.
B. Please modify relative prices according to your actual market conditions.
NO. | ITEM | DETAILS |
1 | DAILY CAPACITY | 10MT |
2 | Raw Materials | Waste tyres |
3 | Cost of tyres | 10T*1500¥/MT=15000¥ |
4 | Cost of Catalyst | 10MT*0.3%*5000¥/MT=150¥ |
5 | Labor (DAILY) | 4P*150¥/D/P=600¥ |
6 | Electricity & Water | 200¥ |
7 | FUEL COST | 0.45MT*1200¥/MT=540¥ |
8 | Other | 100¥ |
9 | Total Cost | 16,590.00¥ |
10 | Oil Income | 10MT*40%*4300¥/MT=17,200.00¥ |
11 | Steel Income | 10MT*13%*1400¥/MT=1,820.00¥ |
12 | Carbon Income | 10MT*35%*300¥/MT=1,050.00¥ |
13 | Gross Income | 20,070.00¥ |
14 | Daily Net Income | 20,070.00¥−16,590.00¥=3,480.00¥ |
15 | Monthly Net Income | 3,480/Day*25D=87,000.00¥ |
16 | Yearly Net Income | 87,000.00¥/M*11M=957,000.00¥ |
Packaging & Shipping
1.Packaging Detail:
All the goods are packed according to export standard with no pollution:
2. Shipping Detail: 30 days after first deposit
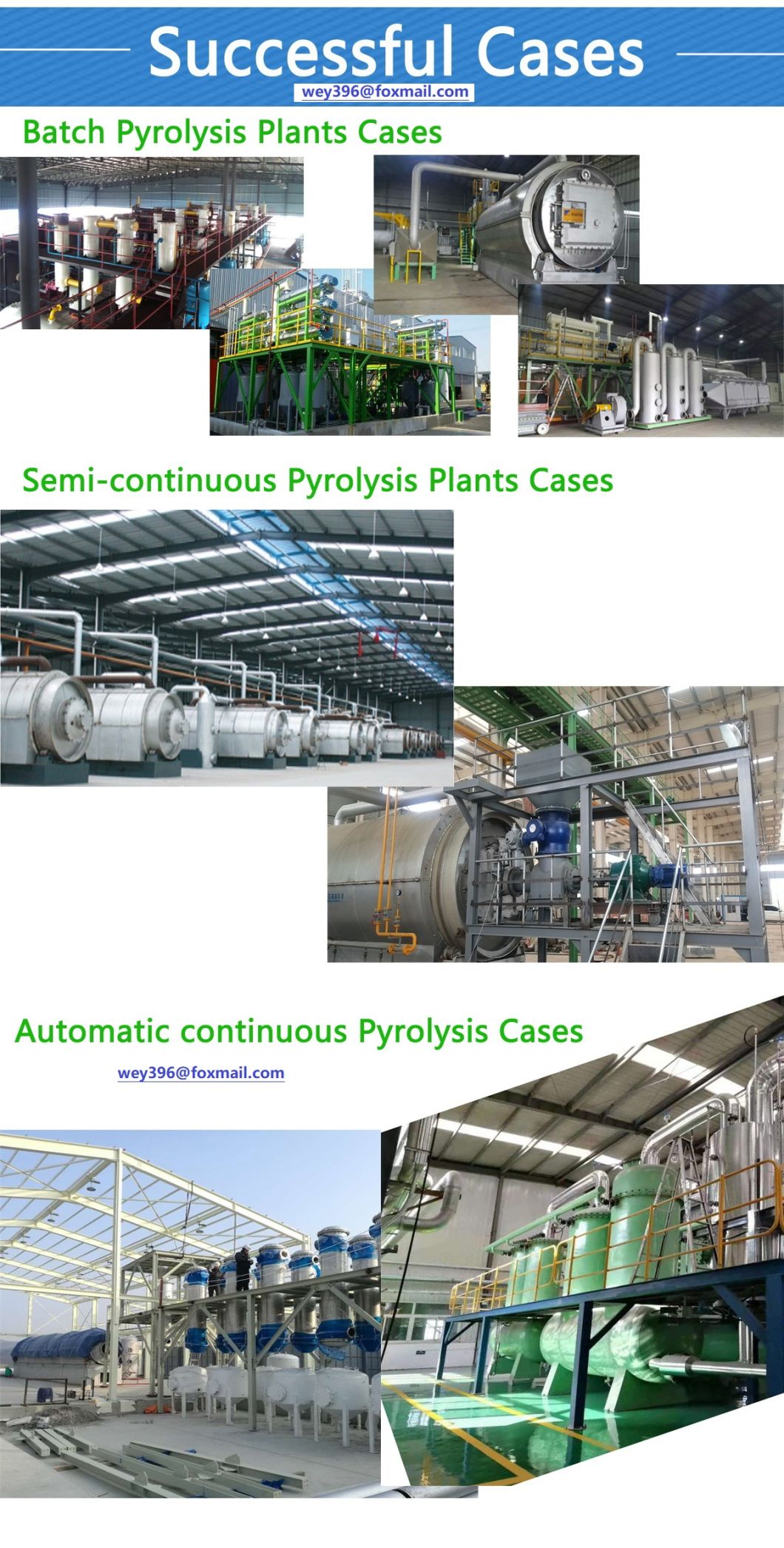
Our Services
Pre-sales Service:
The wide product range enables us to provide our customers with machines or
Complete processing plants.Based on our customers' request and budget, our experts make efficient,
Reliable solutions.Following customers' order we produce strictly, what's more, before placing
The order every customer has the chance to visit working machines or complete plant in the site.
After-sales Service:
1.Quality warranty period: One year warranty for the reactor ,and lifetime maintenance for complete set of machines. pay the double air tickets, accommodation and food.
2.According to the requirement of the buyer, our company sends engineers for installation and commissioning in buyer's site including the training of skills of buyer's workers on operation, maintenance, etc.
3.Supply layout according to buyer's workshop and land, civil works information, operation manuals, etc. to the buyer.
4. For the damage caused by the users, our company provides the parts and accessories with cost price.
5. Our factory supplies the wearing parts with the cost price to clients.

Please contact at: +86-370-2036008.